ความท้าทายอย่างบ้าระห่ำสู่
การควบคุมการเปลี่ยนรูปเนื่องจากความร้อนของเครื่องจักรและสภาวะแวดล้อมรอบเครื่องจักร
เพื่อที่จะตัดเฉือนด้วยความแม่นยำสูง มันจำเป็นต้องจัดการกับการเปลี่ยนรูปเนื่องจากความร้อนต่างๆที่เกิดขึ้นระหว่างการตัดเฉือน และเพื่อที่จะตัดเฉือนด้วยความรวดเร็ว มันจำเป็นต้องจัดการกับการสั่นสะเทือน อย่างไรก็ตาม ในประวัติศาสตร์อันยาวนานของเครื่องจักรแมชชีนทูล ปัญหาของ "ความร้อน" และ "การสั่นสะเทือน" นั้นยากมากและถูกมองว่าเป็นปัญหาที่ไม่มีวันสิ้นสุด
โดยเฉพาะอย่างยิ่งความร้อนเป็นปัญหาที่ยุ่งยาก เครื่องจักรแมชชีนทูลส่วนใหญ่ทำจากเหล็กหรือเหล็กหล่อซึ่งจะขยายตัวหนึ่งในร้อยมิลลิเมตรต่อความยาว 1 เมตรเมื่ออุณหภูมิสูงขึ้น 1 °C ในระหว่างการตัดเฉือน ตัวเครื่องจักรจะขยายตัวเนื่องจากความร้อนที่เกิดจากสปินเดิลและอุปกรณ์ต่อพ่วง นอกจากนี้ ในสภาวะแวดล้อมโรงงานทั่วไป เป็นเรื่องธรรมดาทั่วไปที่อุณหภูมิของสภาวะแวดล้อมจะมีการเปลี่ยนแปลงประมาณ 10 °C ซึ่งจะเปลี่ยนแปลงรูปร่างของเครื่องจักรและส่งผลต่อความแม่นยำในการขึ้นรูป ผู้ผลิตเครื่องจักรแมชชีนทูลต่างๆพยายามที่จะหามาตรการเพื่อลดความร้อนของสปินเดิลและอุปกรณ์ต่อพ่วงด้วยน้ำยาหล่อเย็น แต่นี่ไม่ใช่วิธีการแก้ปัญหาที่แท้จริง
ภายใต้สถานการณ์ดังกล่าว ในประมาณปี พ.ศ.2537 เราได้พัฒนาระบบชดเชย (TAS-S: Thermo Active Stabilizer - Spindle) ซึ่งเป็นเทคโนโลยีพื้นฐานที่วิเคราะห์และชดเชยการเปลี่ยนรูปเนื่องจากความร้อนของสปินเดิล เราได้ไปเยี่ยมเยียนลูกค้าที่ขึ้นรูปแม่พิมพ์ด้วยเครื่องแมชชีนนิ่งเซ็นเตอร์ที่ติดตั้ง TAS-Sเพื่อสำรวจผลลัพธ์ จากการสำรวจ เราพบว่า “การขจัดการเปลี่ยนรูปเนื่องจากความร้อนของสปินเดิลเพียงอย่างเดียวไม่เพียงพอ หากไม่ใช่บริษัทขนาดใหญ่ การสร้างห้องที่มีอุณหภูมิคงที่หรือสิ่งอำนวยความสะดวกอื่นๆ จะไม่สามารถทำได้ หากเครื่องจักรสามารถสร้างความแม่นยำในการขึ้นรูปที่มีเสถียรภาพเท่ากับ 10 µm หรือน้อยกว่าในสภาวะแวดล้อมปกติ งานปรับชดเชยขนาดจะทำได้ง่ายกว่านี้ ... " คือเสียงที่ผมได้ยินจากลูกค้า และนั่นก็เป็นแรงบันดาลใจที่ยอดเยี่ยมสำหรับทีมพัฒนา อย่างไรก็ตาม มันเป็นความท้าทายที่บ้าระห่ำที่จะสร้างเครื่องจักรที่สามารถให้ความแม่นยำเชิงมิติที่มีเสถียรภาพในโรงงานซึ่งมีการเปลี่ยนแปลงของอุณหภูมิตลอดเวลา และความมุ่งมั่นที่จะทำให้ความท้าทายนั้นประสบความสำเร็จถูกมองเป็นเรื่องเพ้อเจ้อโดยคนที่อยู่รอบตัวพวกเรา
ความสำเร็จถูกจุดชนวนขึ้นโดยการเปลี่ยนแปลงอย่างสิ้นเชิง
ของวิธีการคิด
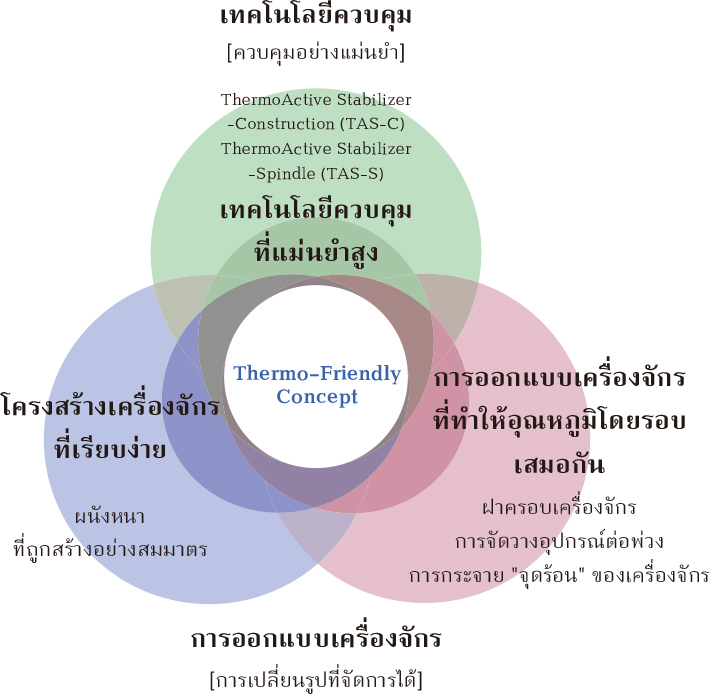
เป็นเวลาหลายปีที่พวกเราวิเคราะห์เรื่องของความร้อนและโครงสร้างของเครื่องจักรโอคุม่ารุ่นต่างๆในห้องทดสอบควบคุมสภาวะแวดล้อม และจากข้อมูลจำนวนมากที่เราเผชิญทำให้เรามั่นใจว่าการทำความเย็นเครื่องจักรที่เป็นแหล่งกำเนิดความร้อนและการใช้เครื่องปรับอากาศอย่างครอบคลุมและหุ้มฉนวนจะทำให้เครื่องจักรซับซ้อนขึ้นและมีราคาแพงขึ้นเท่านั้น แทนที่จะทำเช่นนั้น มันดูมีเหตุผลทางตรรกะมากกว่าที่จะค้นหาโครงสร้างเครื่องจักรที่สามารถจัดการกับความร้อนและการเปลี่ยนรูปเนื่องจากความร้อนที่เกิดขึ้นได้ง่ายขึ้น เป็นการเปลี่ยนแปลงวิธีการคิด; ไม่ยับยั้งการเกิดความร้อน แต่ยอมรับและ “เป็นเพื่อน” (เป็นมิตรกับความร้อน)
ด้วยวิธีการคิดนี้ เราจึงมาถึง Thermo-Friendly Concept ① การออกแบบโครงสร้างเครื่องจักรให้เรียบง่ายที่ทำให้การเปลี่ยนรูปเนื่องจากความร้อนตรงไม่โค้งงอ ② ให้ความสำคัญอย่างระมัดระวังกับการจัดวางแหล่งกำเนิดความร้อนและความสมดุลของอุณหภูมิ และ ③ ระบบที่ควบคุม (ชดเชย) การเปลี่ยนรูปเนื่องจากความร้อนในเรียลไทม์ - ได้เริ่มการผลิตเชิงพาณิชย์ในเครื่องแมชชีนนิ่งเซ็นเตอร์แบบแนวตั้ง MB-46VA ของเรา
หลายคนยังคงเข้าใจผิด การควบคุมการเปลี่ยนรูปเนื่องจากความร้อน “ไม่ใช่เทคโนโลยีที่ตรวจวัดปริมาณความร้อนที่เกิดขึ้นแล้วชดเชยการเปลี่ยนรูปเนื่องจากความร้อนที่ซับซ้อน” แต่เป็น“การออกแบบเชิงกลที่ประณีตตามสมมติฐานหลักที่ว่าการเปลี่ยนรูปเนื่องจากความร้อนที่สมดุลจะถูกควบคุมได้ง่ายยิ่งขึ้น และด้วยวิธีนี้เราจะสามารถจัดการการเปลี่ยนรูปเนื่องจากความร้อน เป็นเทคโนโลยีที่ทำให้ความแม่นยำเชิงมิติของการตัดเฉือนมีเสถียรภาพ”
ขอบคุณที่ MB-46VA ซึ่งประสบความสำเร็จในการควบคุมให้การเปลี่ยนแปลงเชิงมิติเท่ากับ 8 µm เมื่อเวลาผ่านไป ผลลัพธ์ดังกล่าวได้รับการต้อนรับด้วยความประหลาดใจ และได้รับกระแสตอบรับที่ดี อาทิเช่น “งานปรับชดเชยเชิงมิตินั้นลดลงอย่างมากและมั่นใจได้ถึงความแม่นยำ—อุ่นใจมาก” นอกจากนี้บริษัทคู่แข่งยังได้กล่าวอีกว่า “เป็นการเปลี่ยนการเปลี่ยนรูปเนื่องจากความร้อนซึ่งเดิมเป็นเรื่องเคลมให้กลายเป็นเทคโนโลยีที่สร้างผลกำไรได้; ซึ่งเป็นเรื่องที่น่าอัศจรรย์มาก”
ขยายไปสู่เครื่องจักรรุ่นต่างๆพร้อมทั้งพัฒนาต่อไปอย่างต่อเนื่อง
ด้วยผลตอบรับที่ได้จาก MB-V เป็นแรงผลักดัน เราจึงได้ขยายการติดตั้ง Thermo-Friendly Concept ไปยังเครื่องจักรขึ้นรูปหลายภารกิจ เครื่องจักร 5 แกน และเครื่องแมชชีนนิ่งเซ็นเตอร์แบบเสาคู่ แต่จุดเปลี่ยนจริงๆของวิวัฒนาการนี้ คือการประยุกต์ไปสู่เครื่องจักรขึ้นรูปหลายภารกิจและเครื่องจักรขนาดใหญ่ของเรา (DCMC)
สำหรับเครื่องจักรขึ้นรูปหลายภารกิจ การเปลี่ยนรูปเนื่องจากความร้อนมีความซับซ้อนเนื่องจากการเพิ่มขึ้นของแหล่งกำเนิดความร้อนจากสปินเดิลกัด การเคลื่อนไหวของ
เทอร์เรทบน/ล่าง และสปินเดิลของฝั่งตรงข้าม หากวิธีการชดเชยการเปลี่ยนรูปเนื่องจากความร้อนแตกต่างกันในแต่ละเครื่อง ผลที่ต้องการจะไม่สามารถถูกทำให้บรรลุได้
ดังนั้นเราจึงตัดสินใจที่จะสร้างวิธีการที่จะรักษาสมดุลของการเปลี่ยนรูปเนื่องจากความร้อนได้อย่างยอดเยี่ยมไม่ว่าจะเป็นเครื่องรุ่นใดก็ตาม เรามีความก้าวหน้าอย่างมาก
โดยการพัฒนาเทคโนโลยีที่สามารถทำให้การควบคุมง่ายขึ้นโดยใช้การวิเคราะห์ข้อมูลและการวัดจำนวนมากในการออกแบบเครื่องจักร
ในการพัฒนา TFC สำหรับเครื่องจักรเสาคู่ของเรา เราวางชิ้นงานบน DCMC ที่ความสูง 2 ถึง 3 เท่าของความสูงของ VMC ของเรา และพื้นที่โต๊ะงานเป็น 36 เท่า และพบกับความท้าทายในการคิดค้นการควบคุมการเปลี่ยนรูปเนื่องจากความร้อนด้วยเป้าหมายความแม่นยำในการขึ้นรูปที่ 20 µm ในระหว่างการพัฒนา เราไม่มีห้องควบคุมความร้อนที่สามารถใช้ในการทดสอบเครื่องจักรขนาดใหญ่ได้ และเราเผชิญกับความยากลำบากในการวัดการเปลี่ยนแปลงรูปร่างและการขยายตัวทางความร้อน ในข้อจำกัดเช่นนั้น เราจึงผลักดันตนเองให้เข้าสู่การตรวจสอบทฤษฎีการออกแบบและการควบคุมเครื่องจักรอีกครั้ง เพื่อตรวจสอบทฤษฎีที่เราได้สร้างขึ้นมา ห้องควบคุมความร้อนขนาดใหญ่ได้ถูกสร้างขึ้นมาใหม่และนำมาประเมินผล ซึ่งนำไปสู่การกำเนิดของเครื่อง MCR-BIII หลังจากเยี่ยมเยียนลูกค้า 32 ราย เราสามารถยืนยันได้ว่าเครื่องจักร 39 เครื่องสามารถตอบสนองความต้องการด้านสภาวะแวดล้อมของพวกเขาได้ ผลลัพธ์ขององค์ความรู้ที่ได้รับจากความเจ็บปวดในตอนพัฒนา คือขนาดมีเสถียรภาพแม้จะเป็นชิ้นงานขนาดใหญ่และใช้งานได้ดีมากแม้กระทั่งรอยไม่เรียบในการขึ้นรูปก็ไม่เกิดขึ้นแม้จะใช้งานเป็นเวลานาน
ยอดจำหน่ายสะสมและจำนวนรุ่นของเครื่องจักรที่ติดตั้ง Thermo-Friendly Concept
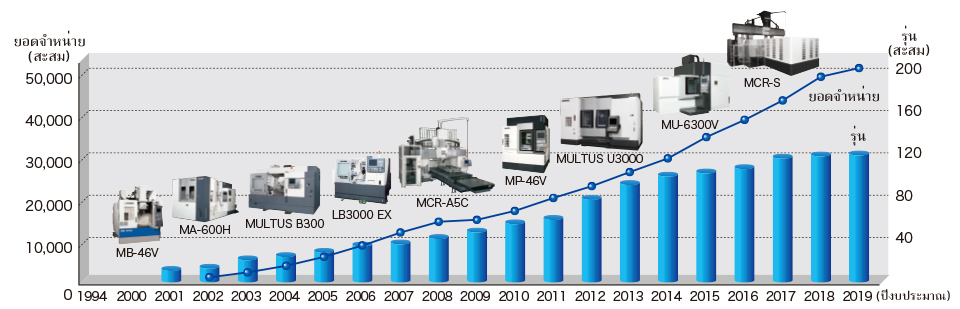
การพัฒนาเทคโนโลยีอัจฉริยะ
สำหรับยุคแห่งการขึ้นรูปอัตโนมัติแบบไร้คนควบคุม
โอคุม่าได้จัดเตรียม 5 เทคโนโลยีอัจฉริยะ (Thermo-Friendly Concept, Collision Avoidance System, Machining Navi, 5-Axis Auto Tuning System,
และ ServoNavi) ซึ่งเป็นฟังก์ชั่นที่มีส่วนช่วยในการปรับปรุง "โครงสร้างพื้นฐานในการขึ้นรูป" ของลูกค้า ในความเป็นจริง ตอนที่ Thermo-Friendly Concept
ถูกพัฒนาขึ้น ฟังก์ชั่นเหล่านี้ส่วนใหญ่จะถูกคาดหวังว่าจะเป็น “การมาของยุคแห่งการขึ้นรูปอัตโนมัติแบบไร้คนควบคุม ในยุคดังกล่าว ผู้ผลิตเครื่องจักรแมชชีนทูล
ควรเตรียมฟังก์ชั่นอะไรบ้าง” คำถามดังกล่าวถูกอภิปรายอย่างละเอียดเพื่อจัดการเทคโนโลยีพื้นฐานให้เป็นระบบอย่างมีประสิทธิภาพ ในความเป็นจริง เราได้บรรลุ
ผลสำเร็จในการพัฒนาฟังก์ชั่นเหล่านั้นมาตามลำดับ
ยกตัวอย่างด้วยเครื่องจักร 5 แกน สปินเดิลที่หมุนจะเอียงไม่ว่าการควบคุมการเปลี่ยนรูปเนื่องจากความร้อนจะดีเพียงใด ดังนั้นเราจึงได้พัฒนา 5-Axis Auto Tuning System ขึ้นเพื่อที่จะปรับแก้ความผิดพลาดทางเรขาคณิตได้อย่างง่ายดาย เครื่องรุ่น MU-500V ซึ่งติดตั้งด้วย Thermo-Friendly Concept เป็นครั้งแรกสำหรับเครื่องจักร 5 แกนได้รับกระแสตอบรับเป็นอย่างดี แต่เมื่อใช้ร่วมกับ 5-AATS แล้วความแม่นยำและเสถียรภาพในการขึ้นรูปดีเพิ่มขึ้นอย่างมีนัยสำคัญ
นอกจากนี้ Machining Navi ยังมี "การควบคุมการสะท้านในการกลึง" ซึ่งถูกกล่าวกันว่าเป็นเรื่องที่ยาก ที่จะนำเครื่องจักรไปสู่สภาวะการตัดที่เหมาะสมที่สุดและช่วยแก้ปัญหาการสะท้านซึ่งเป็นฟังก์ชั่นที่ขาดไม่ได้สำหรับชิ้นงานที่มีลักษณะยาวและงานขึ้นเกลียว
ในช่วงเวลาประมาณ 20 ปีนี้ Thermo-Friendly Concept ได้กลายเป็นคำสรรพนามแทนคำว่า "เทคโนโลยีที่มีผู้ที่ทำได้เพียงหนึ่งเดียว" ของโอคุม่าและได้รับการติดตั้งในเครื่องจักร 83 รุ่นจาก 127 รุ่น ณ เดือนตุลาคม พ.ศ.2562 โดยมียอดจำหน่ายเกิน 50,000 เครื่อง อย่างไรก็ตาม ตัวเลขนี้ยังมีขนาดเล็กเมื่อเทียบกับจำนวนของเครื่องจักรแมชชีนทูลทั่วโลก และเราจะดำเนินการพัฒนาเทคโนโลยีอัจฉริยะในระดับที่สูงขึ้นต่อไปโดยการนำเสนอ "การขึ้นรูปที่เร็วและแม่นยำยิ่งขึ้น" สำหรับการใช้งานที่มีความซับซ้อนมากขึ้น
- กรรมการบริหาร ผู้จัดการฝ่ายเทคโนโลยีและผู้จัดการทั่วไปแผนกวิจัยและพัฒนา
Harumitsu Senda - เข้าร่วมกับโอคุม่าในปี พ.ศ.2530 สำเร็จการศึกษาปริญญาเอก (วิศวกรรมศาสตร์) จากบัณฑิตวิทยาลัยสาขาวิทยาศาสตร์และเทคโนโลยี มหาวิทยาลัยโกเบ หลังจากเข้าร่วมกับโอคุม่าแล้วก็ได้ทำงานด้านเทคโนโลยีการขึ้นรูปที่มีความแม่นยำสูงมากในฐานะผู้พัฒนาเทคโนโลยีพื้นฐาน อาสาทำการวิจัยการเปลี่ยนรูปเนื่องจากความร้อน พัฒนาระบบชดเชยการเปลี่ยนรูปเนื่องจากความร้อนสำหรับสปินเดิลหลัก
สิ่งนี้นำไปสู่การพัฒนาเป็นระบบชดเชยการเปลี่ยนรูปเนื่องจากความร้อนของเครื่องจักรแมชชีนทูล, ซึ่งได้รับรางวัลสมาคมวิศวกรเครื่องกลญี่ปุ่น ปีพ.ศ.2545 หลังจากนั้นในฐานะผู้นำกลุ่ม เขาได้เริ่มวิจัยและพัฒนาการควบคุมการเปลี่ยนรูปเนื่องจากความร้อน และสนับสนุนงานพัฒนาเทคโนโลยีอัจฉริยะของโอคุม่า เลื่อนขั้นเป็นผู้จัดการแผนกวิจัยและพัฒนาในปี พ.ศ.2554, เป็นเจ้าหน้าที่บริหาร รองผู้จัดการฝ่ายเทคโนโลยีสำนักงานใหญ่ควบผู้จัดการแผนกเทคโนโลยีคานิในปี พ.ศ.2557, เป็นเจ้าหน้าที่บริหาร ผู้จัดการฝ่ายเทคโนโลยีสำนักงานใหญ่ควบผู้จัดการแผนกวิจัยและพัฒนาในปี พ.ศ.2559, ดำรงตำแหน่งปัจจุบันในปี พ.ศ.2560 กำกับดูแลด้านเทคโนโลยีและการวิจัยและพัฒนาของโอคุม่า